A walk down the street and shopping places is a good illustration on the huge amount of beverages and liquid products on the market. Despite this, more liquid products keep entering the markets since the demand is ever increasing. New designs and models of bottle filling machines have to be developed to keep up with this demand. There is pressure on filling machine manufacturers to make flexible equipment that handles a variety of products without too much capital investment.
In an effort by Manufacturers of liquid and paste formulations to maximize efficiency, many have turned to high capacity and more automated equipment that deliver the required flexibility.
Important Benefits of Liquid Filling Machines
- Achieve accuracy,
- Reduce product waste,
- Reduce change over times
- Achieve the required sanitation.
Product versus Bottle Filler Characteristics
When installing a bottle filling machine or tube filling Machine, the exact characteristics of the product are a good guide to the equipment to choose.
- A free-flowing liquid product may work better with a timed flow fill machine where the volume delivered per cycle is the same.
- In a viscous product, a positive displacement bottle filling machine may work better.
- Products needing special attention to reduce microbial contamination and guarantee food safety may use hot fill technology to achieve aseptic conditions.
- Some products may change in characteristics when forced through small outlets and require the filler to handle them gently when they flow through the valves.
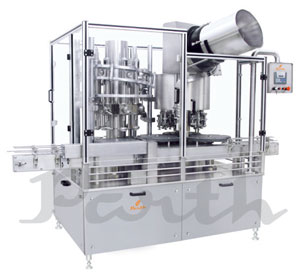
Tube filling machines are used for liquid and paste packaging in tube packages. These can be applied to various products including creams, cosmetics, adhesives, sealants, greases, and some pharmaceuticals. There are various types of tube filling machines based on operation models.
- The fully automatic tube filler has all its functionalities automated and human operation is minimal. The equipment is best for large scale production facilities.
- Semi-automatic filling systems; this machine handles lesser volume compared to the fully automatic model. Machine operation is done by a dedicated operator.
- Rotary tube filler machine; this is a versatile model applicable in most filling industries and can be manufactured as semi-automatic or fully automatic. The machine can also combine various functions such as sealing, batch coding and ejecting all in one cycle. In this way, you are able to cut costs and achieve efficiency with one equipment.
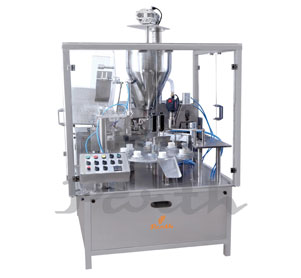
Components of Liquid filling machines
Frame: This provides the support and mounting of the other parts. Some equipment is mounted on the standard portable frame while others use customized and modified frames. The frame is important in ensuring machine stability during transport, installation, and operation.
Tank
This is also a major component of the bottle and tube filler machines. Various designs and dimensions of tanks are applied depending on the individual machine characteristics. For example, an overflow filler uses a recirculation tank to resupply product obtained from overflow nozzles, while a gravity bottle filler machine uses a product supply tank mounted on top of nozzles.
Product Pathway and Noozles
This is the delivery system for the product to bottles or tubes. The components differ from model to model and product to product. Tubing material may also vary to accommodate different product lines and capacities. The noozles are at the end of the pathways and discharge product into the container.Noozle sizes and types may change based on the filling principle, type of container and product specifications.