In today’s pharmaceutical manufacturing landscape, where accuracy, efficiency and hygiene are vital, tube filling lines have become an essential component. These systems play a critical role in ensuring precise dosage, contamination-free packaging and high-speed production. A tube filler machine-can help pharmaceutical manufacturers meet rising demands without compromising on quality.
Let’s dive into the various ways in which these systems are applied in the pharmaceutical space.
Streamlining Ointment and Cream Packaging
One of the most common applications of tube filling machines in the pharmaceutical industry is for packaging semi-solid formulations like ointments and creams. These products are often used in topical treatments, requiring consistent dosage and sterility.
Benefits:
- Precise volumetric filling ensures consistent dosage per unit.
- Cleanroom compatibility maintains a sterile environment.
- Low product wastage through accurate filling nozzles and product recovery systems.
By integrating an automatic tube filling machine, pharmaceutical manufacturers can ensure uniform filling and sealing in one streamlined process. This is critical for preserving the product’s shelf life and effectiveness.

Handling Medicated Gels and Topical Fluids
Medicated gels, often used for oral and dermatological treatments, are another important application for tube fillers. These gels are usually high in viscosity, requiring specialized systems that can manage their thickness without disrupting flow consistency.
Why Tube Fillers Excel?
- Adjustable filling pressure and nozzle size to handle different viscosities.
- Integrated heat sealing or crimping options based on tube type.
- Optional batch coding and printing systems for compliance labeling.
Whether it’s an antibacterial gel or a wound-care paste, a tube filling line provides the level of control and cleanliness needed for pharmaceutical-grade packaging.
Multi Head Tube Filling Machine for High-Volume Output
Large-scale pharmaceutical companies often turn to multi head tube filling machines when production demands escalate. These machines can fill and seal up to multiple tubes, supporting a wide range of tube diameters and materials.
Key Features:
- Multiple synchronized heads for simultaneous filling.
- Reduced production time and lower labor costs.
- Flexible handling of laminate, plastic or aluminum tubes.
By adopting these systems, pharmaceutical plants can significantly boost their productivity without sacrificing product integrity.
Benefits Beyond Speed: Why Tube Fillers are Essential?
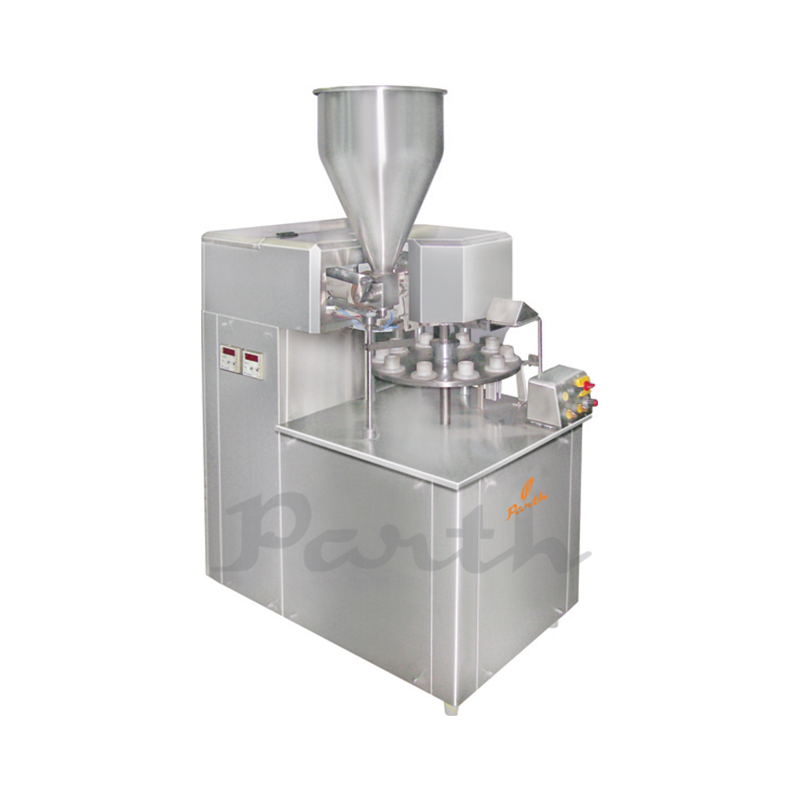
The advantages of using a tube filler machine extend well beyond efficiency. These machines support pharmaceutical operations by enhancing product quality, improving packaging safety and minimizing contamination risks.
Advantages Include:
- Automated controls reduce human error and ensure batch consistency.
- Compact design saves floor space in cleanroom environments.
- Low noise and energy-efficient operation, important in regulated settings.
The automatic single tube filling machine is particularly suited for manufacturers producing multiple formulations. It allows for quick changeovers and minimal cross-contamination risk-ideal for GMP-compliant facilities.
Compliance and Quality Assurance in Tube Filling
Pharmaceutical production is highly regulated and tube filling lines must adhere to international standards like GMP, FDA and EU regulations. Modern tube filling machine manufacturers design systems that support end-to-end compliance.
Compliance Features:
- Integrated data logging for batch traceability.
- Sealing and date coding modules to meet packaging laws.
- CIP/SIP (Clean-In-Place/Sterilize-In-Place) systems for sterile production.
These features not only simplify validation processes but also reduce the time and resources needed for audits and inspections.
Efficiency Gains from Automated Tube Filling Lines
The shift from manual to automatic tube filling machines in pharma manufacturing has led to measurable gains in productivity and reliability. These systems automate critical steps, including:
- Tube feeding and orientation
- Product filling
- Sealing (heat or mechanical)
- Batch coding
- Tube ejection
With reduced dependency on manual labor, manufacturers can lower their operational costs while maintaining higher quality standards.
Adapting to Different Product Types and Viscosities
Another application where tube filling machines shine is their ability to handle a wide variety of pharmaceutical formulations. From light lotions to dense medical pastes, the equipment can be adjusted accordingly.
Adaptability Includes:
- Adjustable filling speeds and volumes.
- Interchangeable parts for different tube sizes.
- Capability to handle shear-sensitive formulations without degradation.
Conclusion
Tube filling lines are more than just automated packaging systems-they are the backbone of efficient, accurate and hygienic pharmaceutical production. Whether it’s a single-head automatic tube filling machine for niche products or a multi-head tube filler for mass production, these systems support both operational excellence and regulatory compliance.
As the pharmaceutical industry continues to innovate and scale, tube fillers will remain central to packaging processes. With their ability to enhance quality, reduce waste and optimize throughput, investing in the right tube filling machine is a strategic move for any manufacturer.
FAQs About Tube Filling LineS
Tube filler machines are commonly used to fill ointments, creams, gels, pastes and lotions into plastic, aluminum or laminate tubes. These machines are ideal for semi-solid pharmaceutical products.
A multi head tube filling machine can typically fill and seal up to multiple tubes, depending on the tube size and the product’s viscosity.
Yes, modern tube filling machines are designed to handle a wide range of viscosities. They can fill everything from light lotions to thick gels without compromising accuracy.
These machines are built using stainless steel and often include clean-in-place (CIP) systems. They operate in a closed environment to minimize contamination and meet pharmaceutical hygiene standards.