In the fast-paced world of pharmaceutical manufacturing, precision and efficiency are paramount. The Automatic Six Head Filling, inner Nozzle pressing cum Pick & Place type Screw Capping Machine emerges as a versatile solution, standing on stainless steel legs with a height adjustment system. Let's delve into the intricacies of this machine and understand its significance in the pharmaceutical industry.
Machine Features
The machine boasts six-head filling capability, ensuring rapid and accurate dispensing of liquid pharmaceuticals. With integrated nozzle fitting and screw capping functionalities, it aligns with current Good Manufacturing Practice (cGMP) standards, ensuring product quality and regulatory compliance.
Machine Construction
Crafted on a sturdy welded powder-coated M.S. Frame structure, the machine's resilience is further enhanced by a complete SS 304 Sheet enclosure. The provision of doors facilitates easy access for maintenance, underlining its robust construction.
Operation Process
Containers move seamlessly on an SS Slat conveyor, guided by a twin pneumatically operated stopper system. This precision prevents spillage during the filling process. The reciprocating nozzles, adjusted for foaming reduction, move gradually from the bottom to the neck of the bottle during filling, ensuring an immaculate process.
Dosing Block
The dosing block, featuring a hexagonal bolt, simplifies the adjustment of fill volume, adding flexibility to the manufacturing process.
Nozzle Pressing
The inner nozzle pressing mechanism operates in a choke feed manner, positioning the pressing accurately on the bottle mouth. The subsequent pressing action ensures a secure and precise fit.
Screw Capping
The screw capping operation involves an infeed star wheel for indexing containers and a rotating head with magnetic torque control. This guarantees a flawless sealing process, crucial for maintaining product integrity.
Importance in Pharmaceutical Industry
Compliance with cGMP standards sets this machine apart, addressing the industry's stringent requirements for quality control. Its precision in filling, nozzle fitting, and screw capping aligns with the high standards expected in pharmaceutical manufacturing.
Advantages of Automatic Filling Machine
The adoption of an automatic filling machine brings several advantages. Increased production speed, reduced human error, and consistent, accurate filling contribute to a more streamlined manufacturing process.
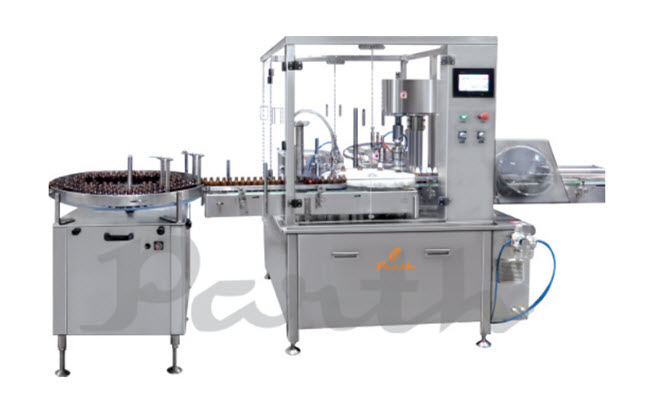
Applications
Primarily designed for eye and ear drop manufacturing, Eye drop filling machine extends its utility to various liquid pharmaceuticals, meeting the diverse needs of the industry.
Industry Trends
As automation becomes integral to pharmaceutical manufacturing, machines like these represent the evolving trends in technology. Continuous advancements aim to enhance efficiency and productivity.
Future Developments
The future holds promise with ongoing innovations in filling and capping technology. Manufacturers can anticipate even more sophisticated solutions that cater to evolving industry demands.
Challenges in Manufacturing
While the benefits are evident, challenges such as maintenance issues and initial investment costs should be acknowledged. Overcoming these hurdles ensures the sustained success of such advanced machinery.
Conclusion
In conclusion, the Automatic Eye/Ear Drop Filling with Nozzle Fitting & Screw Capping Machine cGMP Model stands as a pinnacle of precision and efficiency in pharmaceutical manufacturing. Its construction, operation, and advantages highlight its crucial role in ensuring product quality while meeting the demands of a rapidly evolving industry.