One of the most useful machine tools in any bottling shop is the Bottle Labelling Machine. This nifty little tool creates a virtual pallet for each product. This is an especially good option for companies that ship large volumes of goods since the labels can be easily removed for simple resizing. Each label has a color-coded area for quantity and name. When the roller is pushed to the appropriate place on the pallet, the labelling machine “picks up” the color-coded area and creates a perfectly sized tag for the product. This saves company staff time, reduces waste, and promotes brand loyalty among distributors, manufacturers, and retailers.
Three Types of Labelling Configuration for Bottle Labelling Machine
The three basic label configurations are front-push, vertical-wrap, and back/front. In addition, some machines come with additional features like bottle labels for small B2B loads, full-color labels for graphic arts applications, custom shapes for medical applications, and UV curing capabilities. Of these, the most popular are the front-push, vertical-wrap, and back/front machines. Each type of machine has its advantages and disadvantages. The Bottle Labelling Machine is the only option that combines all three types into one convenient package.
The front-push machine is the simplest, least expensive, and easiest to operate. The person manually rolls the tapered label applicator over the bottles’ necks, creating a uniform border that holds the color-coded labels. The downside is that manual action consumes extra time and energy, and production can be minimal. Furthermore, the roll labels can be manually changed but the process is more complicated. Also, the manual labelling capability is not sufficient for full-scale packaging operations.
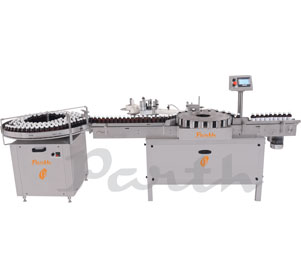
The vertical-wrap and back label applicators are more costly but are more versatile, offer more options, and have faster checks. Vertical wrap uses expandable plastic trays that wrap around the bottles’ sides, allowing them to be stacked or uncut. The back/front label machine has an automated push button that rolls the labels automatically, thereby eliminating the need for manual intervention. These types of bottle labelling machines have an enhanced capacity for international labelling requirements.
The third type, the hot stamp label applicator, is the most innovative and functional. It uses a thermal hot stamp to apply the color-coded labels. With this machine, there is no need to change colored tapes, making it a more compact machine. The drawback is that hot stamps can only apply a limited number of colours, making it a less flexible machine for large volume label applications. The third option, the hot stamp cold transfer applicator, uses the same tray system but operate with a cold thermal transfer process, creating a deeper level of labelling accuracy than its hot stamp counterpart. Although this machine is more expensive and consumes more electricity, its full label applications result in a higher level of label satisfaction due to greater precision and quality.