Dry powder filling machines play a crucial role in pharmaceutical and industrial applications. Whether it's an injectable dry powder filling machine, a sterile powder filling machine or an automatic dry powder filling machine, proper maintenance is key to ensuring efficiency, accuracy and longevity.
In this guide, we will explore expert maintenance practices to maximize the performance of your dry powder filling machine for pharmaceuticals and avoid costly downtime.
The Importance of Dry Powder Filling Machine Maintenance
A well-maintained dry powder filling machine ensures precision, consistency and operational efficiency. Poor maintenance can lead to contamination, breakdowns and increased production costs.
Why Maintenance Matters?
- Prevents mechanical failures.
- Ensures consistent filling accuracy.
- Reduces contamination risks.
- Extends the machine’s lifespan.
- Enhances production efficiency.
Regular upkeep can save time and money while ensuring compliance with industry regulations.
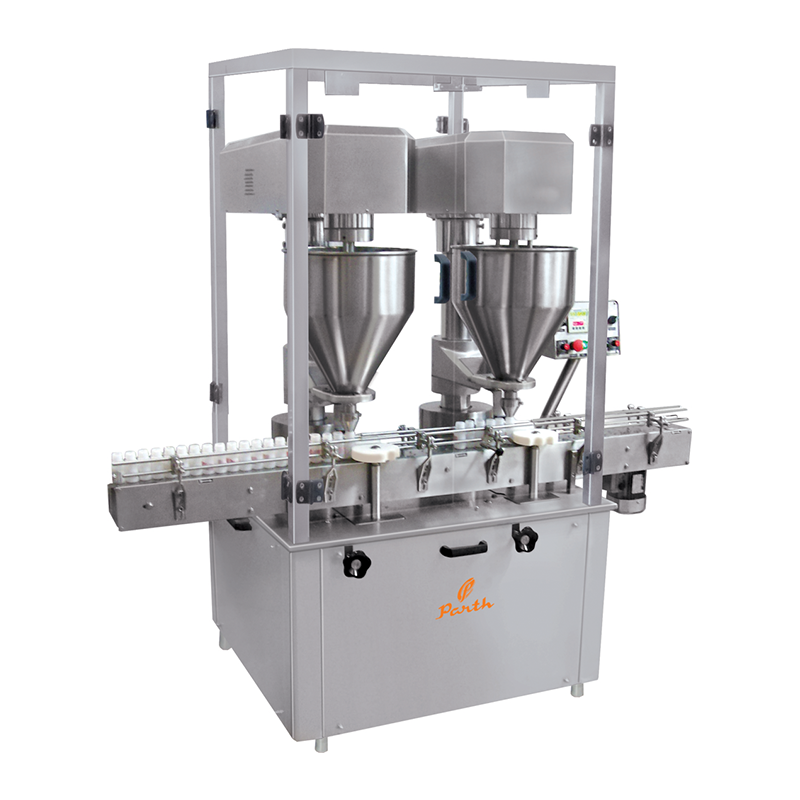
Dry Powder Filling Machine Supports Routine Cleaning and Sanitization
Powder residues can accumulate inside the machine, affecting its efficiency. Proper cleaning protocols must be followed to prevent cross-contamination and machine wear.
Daily Cleaning Best Practices:
- Wipe down external surfaces with a lint-free cloth.
- Remove and clean nozzles, augers and filling components.
- Use compressed air to clear powder buildup in crevices.
- Sanitize contact parts per pharmaceutical regulations.
Regular cleaning keeps your automatic dry powder filling machine running smoothly and prevents contamination.
Dry Powder Filling Lubrication and Wear Prevention
Moving parts in a sterile powder filling machine require proper lubrication to function efficiently. Lack of lubrication can lead to increased friction, wear and overheating.
Lubrication Guidelines:
- Use manufacturer-recommended lubricants.
- Lubricate bearings, gears and sealing components.
- Avoid over-lubrication, as excess grease can attract powder particles.
- Check lubrication levels weekly.
Proper lubrication reduces friction, minimizes wear and extends the machine’s operational life.
Dry Powder Filling Machine: Regular Inspection and Calibration for Pharmaceuticals
Maintaining precise powder-filling accuracy requires routine inspections and calibrations. Over time, minor misalignments can affect dosing accuracy and increase product waste.
Inspection Checklist:
- Check sensors and electrical connections for faults.
- Inspect augers and dosing mechanisms for wear.
- Examine gaskets and seals for cracks.
- Ensure all screws and fasteners are secure.
Calibration Best Practices:
- Verify powder weight accuracy with test samples.
- Adjust filling parameters if necessary.
- Perform calibration at least once a month.
Regular calibration ensures your dry powder filling machine for pharmaceuticals remains accurate and reliable.
Injectable Dry Powder Machine: Managing Environmental Conditions
Humidity and temperature fluctuations can impact powder flow and machine performance. Keeping the environment stable can prevent blockages and inconsistencies.
Ideal Environmental Conditions:
- Maintain a controlled room temperature between 20°C-25°C.
- Keep humidity levels below 50% to prevent powder clumping.
- Install proper ventilation to reduce airborne particles.
A controlled environment enhances the performance and longevity of your injectable dry powder filling machine.
Preventing Contamination and Cross-Contamination Using Dry Powder Filling Machine
In pharmaceutical applications, contamination risks must be minimized. Using the right handling techniques ensures product purity and compliance with industry standards.
Best Practices to Avoid Contamination:
- Use dedicated tools for different powders.
- Clean contact surfaces before switching batches.
- Train operators on contamination prevention protocols.
- Follow GMP (Good Manufacturing Practices) guidelines.
A contamination-free machine ensures safe and high-quality product output.
Dry Powder Filling Machine Offers Training and Operator Best Practices
Well-trained operators reduce operational risks and machine malfunctions. Investing in training ensures the machine is used correctly and maintained properly.
Key Training Areas:
- Proper startup and shutdown procedures.
- Troubleshooting common machine issues.
- Understanding cleaning and lubrication schedules.
- Following manufacturer maintenance recommendations.
A knowledgeable team can maximize the lifespan of your sterile powder filling machine.
Dry Powder Filling Machine Manages Spare Parts
Worn-out parts can lead to downtime and production delays. Keeping essential spare parts on hand minimizes disruptions.
Essential Spare Parts to Stock:
- Seals and gaskets
- Nozzles and augers
- Electrical sensors
- Drive belts and bearings
Stocking critical spare parts ensures quick repairs and uninterrupted production.
Automatic Dry Powder Filling Machine Monitors Performance with Data Tracking
Modern automatic dry powder filling machines often come with data tracking and monitoring features. Utilizing these tools can help detect early signs of wear and inefficiency.
Benefits of Data Tracking:
- Identifies trends in performance decline.
- Detects filling inconsistencies before major failures.
- Helps schedule predictive maintenance.
Using performance data helps improve machine longevity and operational efficiency.
FAQs About Powder Filling Machines
Daily external cleaning is recommended, while deep cleaning should be done weekly to prevent residue buildup and contamination.
Always use manufacturer-recommended lubricants to ensure compatibility with machine components and avoid contamination.
If you notice inconsistent filling weights or product variations, perform a calibration test and adjust settings accordingly.
Maintain a temperature of 20°C-25°C and keep humidity below 50% to prevent powder clumping and machine inefficiency.
Well-trained operators reduce the risk of errors, ensure proper machine use and follow maintenance schedules effectively.
Conclusion
A well-maintained dry powder filling machine for pharmaceuticals can deliver reliable performance for years. Following best practices such as routine cleaning, lubrication, calibration and environmental control ensures longevity and efficiency. Training staff and keeping spare parts ready further enhance operational success.
By investing in proper maintenance, you can reduce downtime, improve accuracy and maximize your injectable dry powder filling machine’s lifespan.