Ensuring the safety of operators and the integrity of pharmaceutical products is paramount when using injectable liquid filling machines. These machines are critical in the pharmaceutical industry for accurately filling vials with liquid medications, and maintaining safety protocols and best practices is essential to prevent contamination, ensure accurate dosing, and protect operators from potential hazards. Below, we detail the necessary safety protocols and provide best practice guidelines for operating vial filling machines safely and effectively.
Safety Protocols for Operating Injectable Liquid Filling Machines
- Personal Protective Equipment (PPE):
- Operators must wear appropriate PPE, including gloves, gowns, masks, and safety goggles, to protect against exposure to hazardous substances and prevent contamination.
- Ensure PPE is donned and doffed correctly to maintain sterility and safety.
- Training and Certification:
- All operators should undergo comprehensive training on the use and maintenance of filling machines.
- Certification programs should be implemented to ensure that operators are proficient in handling the equipment safely.
- Machine Calibration and Maintenance:
- Regular calibration of filling machines is essential to ensure accurate dosing and prevent mechanical failures.
- Implement a routine maintenance schedule to check and replace worn or damaged parts.
- Cleanroom Standards:
- Operate filling machines in a cleanroom environment adhering to ISO class standards to minimize contamination risks.
- Regularly monitor and control cleanroom parameters, including temperature, humidity, and particulate levels.
- Sterilization Procedures:
- Ensure all equipment and components are sterilized before use. Use autoclaves, dry heat ovens, or other sterilization methods appropriate for the materials involved.
- Implement stringent sterilization protocols for vials, stoppers, and any other materials that come into contact with the liquid product.
- Emergency Protocols:
- Develop and regularly update emergency protocols for handling spills, equipment malfunctions, and exposure incidents.
- Ensure all operators are familiar with emergency procedures and know how to use safety equipment like eye wash stations and spill kits.
Best Practices for Ensuring Safety and Product Integrity
- Proper Setup and Operation:
- Ensure the filling machine is set up according to the manufacturer’s guidelines. Check all connections, calibrate the machine, and run test batches to confirm accuracy.
- Use automated systems where possible to reduce human error and enhance precision.
- Quality Control Measures:
- Implement stringent quality control checks at various stages of the filling process, including pre- and post-filling inspections.
- Utilize in-line monitoring systems to detect and correct deviations in real-time.
- Documentation and Traceability:
- Maintain detailed records of each production batch, including equipment settings, operator details, and quality control results.
- Use electronic records and audit trails to ensure complete traceability and accountability.
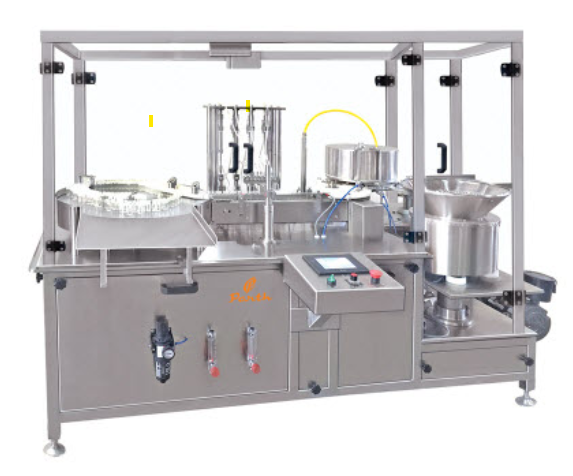
- Environmental Monitoring:
- Continuously monitor the cleanroom environment to ensure it meets the required standards for sterile pharmaceutical production.
- Implement advanced filtration systems, such as HEPA filters, to maintain air quality and minimize particulate contamination.
- Regular Audits and Inspections:
- Conduct regular internal audits to ensure compliance with safety protocols and best practices.
- Schedule periodic inspections by external regulatory bodies to validate the integrity of the production process.
- Waste Management:
- Properly dispose of waste materials, including used vials, stoppers, and any contaminated PPE, according to hazardous waste regulations.
- Implement protocols for the safe handling and disposal of pharmaceutical waste to prevent environmental contamination.
- Continuous Improvement:
- Foster a culture of continuous improvement by encouraging feedback from operators and regularly reviewing safety protocols and procedures.
- Stay updated on industry advancements and integrate new technologies and practices that enhance safety and efficiency.
By adhering to these safety protocols and best practices, pharmaceutical manufacturers can ensure the safe operation of injectable liquid filling machines, protect their operators, and maintain the highest standards of product integrity. Implementing these measures not only safeguards health and safety but also supports regulatory compliance and enhances the overall quality and reliability of pharmaceutical products.