In the dynamic world of packaging, where precision and efficiency are paramount, tube filling machines have emerged as game-changers. From Semi-Automatic Tube Filling and Sealing Machines to Automatic Rotary and Linear Tube Filling Machines, these innovations are reshaping how products are packaged. In this article, we will delve into the various types of tube filling machines, their advantages, selection criteria, maintenance practices, and the future trends that are set to redefine the industry.
I. Introduction
Definition of Tube Filling Machines
Tube filling machines are automated devices designed to efficiently fill and seal tubes with various products, ranging from pharmaceuticals to cosmetics. These machines have become indispensable in the packaging industry, offering a seamless solution for high-volume production.
Importance in Packaging Industry
In an era where consumer expectations for quality and presentation are higher than ever, the role of tube filling machines in ensuring consistent and precise packaging cannot be overstated. As the demand for efficiency grows, manufacturers are turning to these machines to meet the evolving needs of the market.
II. Types of Tube Filling Machines
A. Semi-Automatic Tube Filling and Sealing Machine
1. Features and Benefits
Semi-automatic tube filling machines strike a balance between manual and fully automated processes, providing flexibility and control over the filling and sealing operations. Their versatility makes them ideal for various applications, from pharmaceutical creams to adhesives.
2. Applications
Industries such as pharmaceuticals, cosmetics, and food packaging benefit from the adaptability of semi-automatic tube filling machines. Their ability to handle different viscosities and products makes them a valuable asset in diverse manufacturing settings.
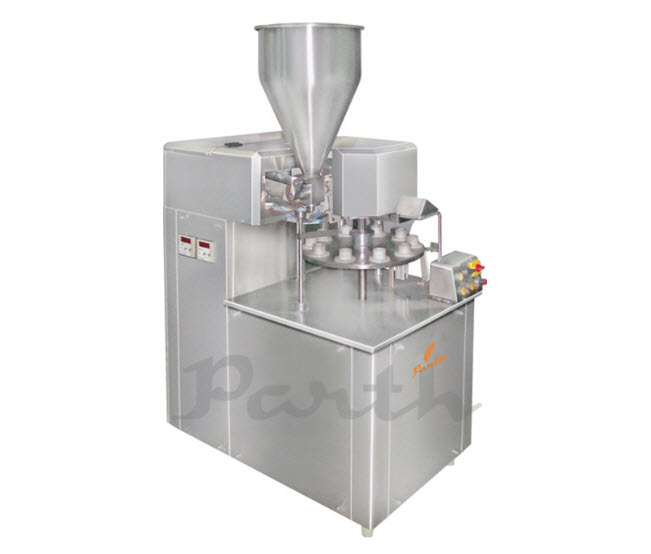
B. Automatic Rotary Tube Filling Machine
1. Operational Mechanism
Automatic rotary machines operate on a continuous basis, maximizing efficiency in high-volume production. These machines employ a rotary indexing system for filling and sealing, ensuring a rapid and streamlined process.
2. Advantages
The speed and precision of rotary tube filling machines make them indispensable for industries with large-scale production requirements. Their ability to handle various tube sizes and configurations enhances their versatility.
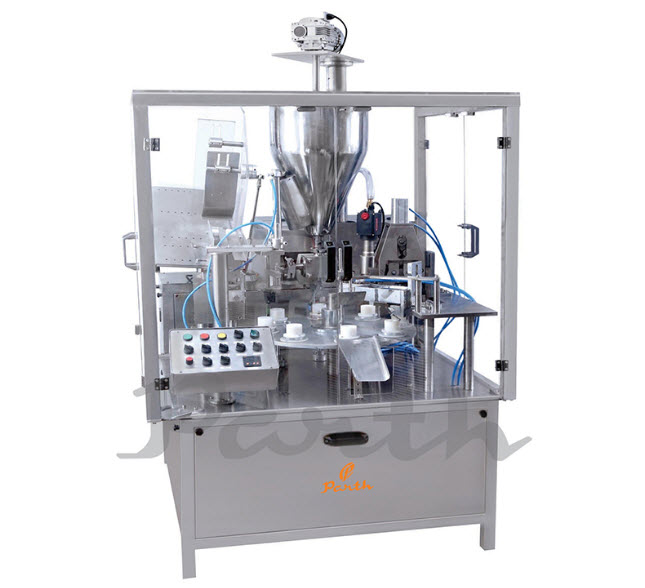
C. Automatic Linear Tube Filling Machine
1. Key Characteristics
Linear tube filling machines provide a linear filling and sealing process, combining speed with accuracy. They are particularly suitable for products with specific packaging requirements.
2. Industries Utilizing
Industries requiring precise and controlled filling, such as pharmaceuticals and cosmetics, find automatic linear tube filling machines instrumental in maintaining product integrity and quality.
III. Advantages of Automatic Tube Filling Machines
A. Efficiency in Production
Automatic tube filling machines significantly reduce the time required for filling and sealing operations, leading to increased production efficiency. This advantage becomes crucial in meeting tight deadlines and coping with market demands.
B. Precision and Consistency
The automated nature of these machines ensures a high level of precision in dosage and product placement. Consistency in packaging not only enhances product quality but also contributes to brand reliability and consumer trust.
C. Versatility
The ability of automatic tube filling machines to handle various product viscosities, tube sizes, and configurations provides manufacturers with the flexibility needed to adapt to diverse production requirements.
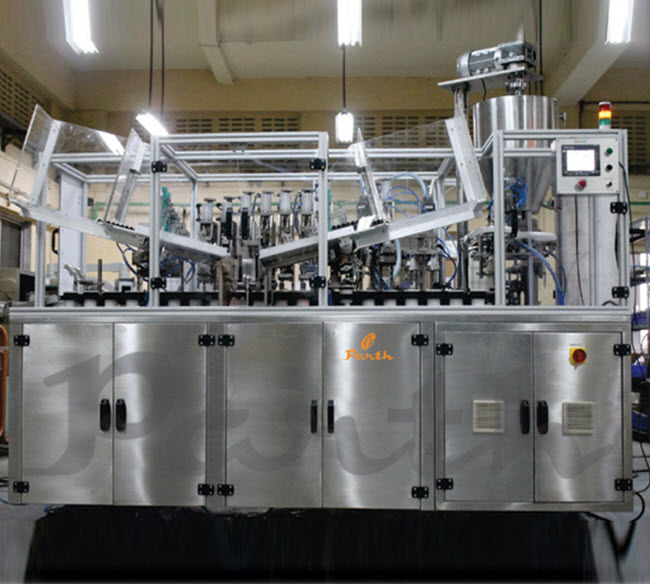
IV. Choosing the Right Tube Filling Machine
A. Factors to Consider
1. Production Volume
Selecting a tube filling machine that aligns with the production volume is critical. Whether it's a semi-automatic machine for small batches or an automatic rotary machine for high-volume production, matching capacity to demand is essential.
2. Type of Products
Different products have unique packaging requirements. Considering factors like viscosity, texture, and packaging material compatibility helps in choosing the right tube filling machine for specific applications.
3. Budget Constraints
While investing in automation can lead to long-term savings, it's essential to consider budget constraints. Finding a balance between upfront costs and long-term benefits ensures a viable investment.
V. Maintenance and Troubleshooting
A. Regular Maintenance Practices
To ensure the seamless operation of tube filling machines, regular maintenance is paramount. Cleaning, lubrication, and routine inspections prevent downtime and extend the lifespan of the equipment.
B. Common Issues and Solutions
Addressing common problems, such as uneven filling or sealing issues, promptly is crucial. Understanding the troubleshooting procedures specific to each type of tube filling machine enhances overall operational reliability.
VI. Future Trends in Tube Filling Technology
A. Automation and Artificial Intelligence Integration
The integration of automation and artificial intelligence is on the horizon, promising even greater efficiency and precision in tube filling operations. Smart machines equipped with predictive maintenance capabilities are set to revolutionize the industry.
B. Sustainable Practices in Tube Filling
As environmental concerns gain prominence, the tube filling industry is witnessing a shift towards sustainable practices. Manufacturers are exploring eco-friendly materials and energy-efficient processes to reduce the environmental impact of packaging.
VIII. Comparison with Traditional Filling Methods
A. Manual Filling vs. Automatic Tube Filling
Drawing a comparison between traditional manual filling methods and automatic tube filling machines emphasizes the significant advantages in terms of speed, accuracy, and efficiency.
B. Speed and Accuracy Comparison
Quantifying the speed and accuracy improvements achieved by automatic tube filling machines provides a clear understanding of their impact on production timelines and product quality.
IX. Regulations and Compliance
A. Industry Standards for Tube Filling Machines
Adhering to industry standards and regulations is crucial for manufacturers. Understanding the compliance requirements ensures that tube filling operations meet the necessary quality and safety standards.
B. Ensuring Compliance in Manufacturing
Implementing quality control measures and documentation processes ensures that tube filling operations comply with regulatory standards. This proactive approach is vital for maintaining product integrity and consumer safety.
XIV. Future Prospects and Growth
A. Market Trends and Predictions
Analyzing market trends and predictions provides valuable insights into the future prospects of tube filling machines. As industries continue to embrace automation, the demand for advanced tube filling technologies is expected to grow.
B. Opportunities for Tube Filling Machine Manufacturers
Identifying opportunities for tube filling machine manufacturers in emerging markets and industries positions them to capitalize on the growing demand for efficient and automated packaging solutions.
Conclusion
Recap of Key Points
In conclusion, tube filling machines represent a revolutionary step forward in packaging efficiency. From semi-automatic to fully automated options, these machines offer precision, consistency, and versatility in meeting diverse production needs.
Encouragement for Implementing Tube Filling Machines
Businesses in various industries are encouraged to explore the benefits of tube filling machines to enhance their packaging processes. Embracing automation not only improves efficiency but also positions companies at the forefront of innovation and competitiveness.